sources of error in rockwell hardness test|rockwell hardness determination : commercial The sources of error to be discussed are: (1) the hardness machine’s lack of repeatability; (2) the non-uniformity in hardness of the material under test; (3) the hardness machine’s lack of .
28 de set. de 2023 · AGRG.cloud understands your business. Only the functions you need. No overpayments. Our solutions are high comfort and safety, low energy consumption, full control of your staff. You don’t need a server, purchase and maintenance of any programs, any staff costs. All you need is wi-fi.
{plog:ftitle_list}
web6 dias atrás · Visit ESPN for Internacional live scores, video highlights, and latest news. Find standings and the full 2024 season schedule.
In the use of hardness test blocks, the uncertainty due to block non-uniformity can be reduced if one is willing to make measurements at specified locations on the blocks. Statistical methods for achieving this reduction are explained in this paper.TableofContents ListofFigures ix ListofTables xii 1.Introduction 1 .
procedures when performing Rockwell hardness measurements and .
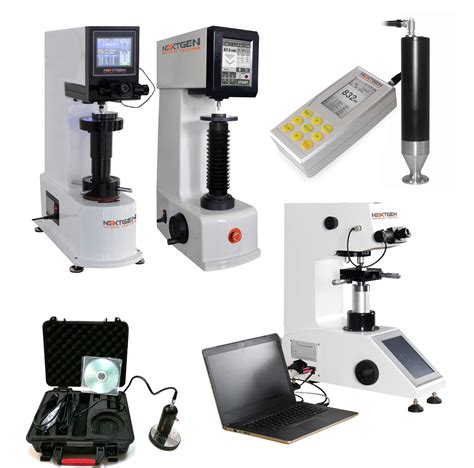
TableofContents ListofFigures ix ListofTables xii 1.Introduction 1 2.RockwellHardnessTest 2 2.1Significanceofthetest 2 2.2Rockwellindentationtestprinciple 2 2 .This document provides guidance for calibration and testing laboratories involved in hardness measurements, as well as their assessors. It has been produced to improve harmonization in .
The sources of error to be discussed are: (1) the hardness machine’s lack of repeatability; (2) the non-uniformity in hardness of the material under test; (3) the hardness machine’s lack of .Step 1- Identifying the parameters for which uncertainty is to be estimated Step 2- Identifying all sources of uncertainty in the test Step 3- Classifying the uncertainty according to Type A or B .
uncertainty in hardness testing machine
Adhering to good practice procedures when performing Rockwell hardness measurements and calibrations is a beneficial step to reducing measurement errors. The .

The Rockwell test consists of measuring the additional depth to which a carbide ball or Brale® diamond penetrator is forced by a heavy (major) load beyond the depth of a previously applied .procedures when performing Rockwell hardness measurements and calibrations is a beneficial step to reducing measurement errors. The purpose of this Guide is to explain the causes of .
With the precise nature of the test (keeping in mind that one Rockwell point on the regular scale equals 0.002 mm or 0.00008 of an inch) a movement of only 0.001 of an inch could cause an error of over 10 Rockwell .
In order to reduce the testing errors in Rockwell hardness of metal specimens and improve the accuracy of hardness testing, several methods had been tried out and examined based on GB/T.
standard hardness of reference block
Numerous aspects of the Rockwell hardness test can influence the measurement result. These include the function and calibration of individual components of the hardness machine, variations in the indenter, the testing cycle that is used, the testing environment, the condition of the test material, and the operator. When considering all of these influences, it seems remarkable that .
The Rockwell hardness test continues to be applied as a tool for assessing . calibrations is a beneficial step to reducing measurement errors. The purpose . Sources of uncertainty for the certified average HRC hardness value with hypothetical values to be usedThe Rockwell hardness test method, as properly defined in ASTM E-18 standards, is the most commonly used hardness test method among all the other methods. + 86 755 61301520 [email protected]
Answer: a Explanation: Brinell hardness test uses a hardened steel ball as an indenter. It is 10 mm diameter ball. Diamond indenter is used in the Rockwell test.The Rockwell hardness test method, as defined in ASTM E-18, is the most commonly used hardness test method. You should obtain a copy of this standard, read and understand the standard completely before attempting a Rockwell test. The Rockwell test is generally easier to perform, and more accurate than other types of hardness testing methods .
Below image shows the general steps in Rockwell hardness indentation measurement/testing. “h” is the difference in the indentation depths, it shows the probable actual rage of the hardness . View lab 1 ( rockwell hardness test ).docx from JKM 31342 at POLITEKNIK SEBERANG PERAI. MECHANICAL ENGINEERING DEPARTMENT TOPIC SESSION JUNE 2020 COURSE DJJ30113 - MATERIAL SCIENCE. AI Chat with PDF. Expert Help. . Discuss the possible sources of errors in Rockwell hardness test.
profiles. The Rockwell test is the most popular indentation hardness test and is used in a wide variety of applications. Advantages of the Rockwell Test There are several reasons for the popularity of the Rockwell test. The test itself is very rapid. On a manually operated unit, a Rockwell test takes only five to ten seconds, The choice is not only between the regular hardness test and superficial hardness test, with three different major loads for each, but also between the diamond indenter and the 1/16, 1/8, 1/4 and 1/2 in. diameter steel ball indenters. In order to reduce the testing errors in Rockwell hardness of metal specimens and improve the accuracy of hardness testing, several methods had been tried out and examined based on GB/T 230 and other relevant inspection specifications, firstly, correct the hardness of testing pieces directly by using the hardness reference blocks to calibrate the .There are two types of Rockwell test (Table 23.1): Rockwell: the minor load is 10 kgf, the major load is 60, 100, or 150 kgf. Superficial Rockwell: the minor load is 3 kgf and major loads are 15, 30, or 45 kgf. Table 23.1: Some common scales in Rockwell and Superficial Rockwell testing
standard hardness determination
There are two types of Rockwell test (Table 23.1): Rockwell: the minor load is 10 kgf, the major load is 60, 100, or 150 kgf. Superficial Rockwell: the minor load is 3 kgf and major loads are 15, 30, or 45 kgf. Table 23.1: Some common scales in Rockwell and Superficial Rockwell testing The Rockwell hardness test continues to be applied as a tool for assessing the properites of a product while the tolerances on the acceptable material hardness have become tighter and tighter. Adhering to good practice procedures when performing Rockwell hardness measurements and calibrations is a beneficial step to reducing measurement errors.

This article explains the procedure to perform the Rockwell hardness test on metals. Rockwell Hardness Test Procedure. The Rockwell hardness test employs the principle of differential-depth method. During the test, the indenter of the equipment is forced to make a residual depth on the test specimen.There are two types of Rockwell test (Table 23.1): Rockwell: the minor load is 10 kgf, the major load is 60, 100, or 150 kgf. Superficial Rockwell: the minor load is 3 kgf and major loads are 15, 30, or 45 kgf. Table 23.1: Some common .measured using a depth-measuring system integrated into the Rockwell hardness testing machine. The Rockwell hardness test employs different combinations of test loads and indenters to accommodate various material hardness levels. The most commonly used scales are Rockwell B (HRB) and Rockwell C (HRC), each with specific test parameter. 5. In the use of hardness test blocks, the uncertainty due to block non-uniformity can be reduced if one is willing to make measurements at specified locations on
In the Rockwell hardness test, a differential-depth method, the residual depth of the indent made by the indenter is measured. In contrast, the indentation size is measured in the Brinell, Vickers and Knoop optical test methods.ACKNOWLEDGMENTS Theauthorwouldliketothankthefollowingpersonsforsharingtheir experienceandprovidinginformationforthisGuide.Theirinputandreview .Description of Rockwell Test; ASTM A 370 says: “In this test a hardness value is obtained by determining the depth of penetration of a diamond point or a steel ball into the specimen under certain arbitrarily fixed conditions. A minor load is first applied which causes an initial penetration, sets the penetrator on the material and holds it The Rockwell hardness test involves applying a sequence of loads to the material and measuring the depth of the resulting indentation, which indicates the material’s hardness. . and avoid parallax errors by ensuring the measurement is taken directly over the indentation. . Material hardness measured using a Vickers hardness tester (Source .
tuv paint test
A Rockwell hardness tester. The Rockwell scale is a hardness scale based on indentation hardness of a material. The Rockwell test measures the depth of penetration of an indenter under a large load (major load) compared to the penetration made by a preload (minor load). [1] There are different scales, denoted by a single letter, that use different loads or indenters. In the Rockwell hardness test, the measure of the hardness is not an indentation surface but an indentation depth. Either a carbide ball or a rounded diamond cone with a tip angle of 120° and a tip radius of 0.2 mm serves as the indenter. The indentation depth can be read directly from a dial gauge via the traverse path of the testing machine.
Rockwell hardness machine’s measurement “error” determined as part of an indirect verification [2,3]; (2) Rockwell hardness values measured during normal testing; and (3) the certified calibration value of Rockwell hardness reference blocks. Rockwell hardness is determined by measuring the distance traveled by an indenter when a heavy load is applied to a heat treated part. Variants on the Rockwell hardness test procedure are used depending on the material and strength of a part.
What is Rockwell hardness testing? The Rockwell Hardness Test is generally a non-destructive test performed on samples when it’s necessary to determine how hard a material is. It’s generally considered easier to perform compared to other methods, like Vickers or Brinell hardness testing. Another advantage is the small area of indentation needed to carry out the . The calibration conditions concerning hardness test blocks used for the verification of hardness testing machines for the Rockwell test were modified by the International Standardization Organization.
lead paint test uk
Link vào 188BET không bị chặn mới nhất tháng 3/2024. 188BET LINK MOBILE. 188BET LINK DESKTOP. Ưu đãi hấp dẫn dành cho thành viên mới : Tặng ngay 100% giá trị nạp lần đầu ( Xem hướng dẫn đăng ký ) Hoàn trả 0.38% thể thao & 0.76% casino không giới hạn. 188Bet App là đại lý chính thức .
sources of error in rockwell hardness test|rockwell hardness determination